Etape 2 : les hauts fourneaux et les aciéries
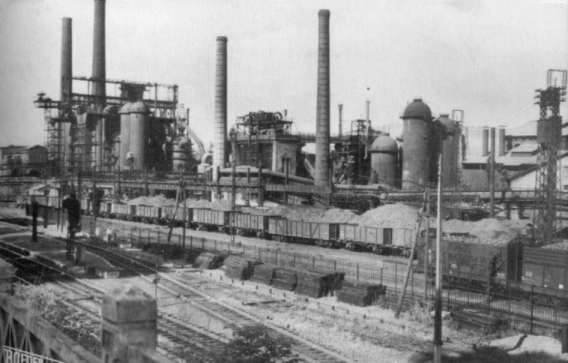
Les hauts fourneaux
Avec les longues cheminées et leurs épaisses fumées, les hauts fourneaux sont les symboles par excellence de l’usine. Leur rôle premier est de produire de la fonte à partir du minerai de fer. On cherche premièrement à désoxyder le minerai, c’est-à-dire à extraire le fer qu’il contient.
Au nombre de deux lors de la création de l’usine en 1872, les Hauts fourneaux sont alors à la pointe de la technologie. Les hauts-fourneaux du XIXe siècle sont très proches de ceux que l’on utilise de nos jours. A l’intérieur du fourneau, on entrepose du minerai de fer concassé et du charbon minéral appelé coke par couches, le charbon jouant le rôle de combustible très riche en carbone.
Le haut fourneau peut atteindre trente mètres de haut. Il est chargé en minerai de fer et en coke par le haut (gueulard). En bas, "la ceinture de vent" apporte de l’air chaud provenant d’une tour de Cowper. La température dans le ventre atteint les 1800°C.
A cette température, les oxydes de fer du minerai, mélangés au coke se transforment en fonte. Quant à la roche du minerai, elle se transforme en laitier. Tout en bas, au creuset, un trou de coulée permet de faire sortir la fonte liquide, un autre trou permet d’évacuer le laitier qui flotte au-dessus de la fonte. Une fois refroidi et solidifié, le laitier est utilisé pour la fabrication du ciment ou comme remblai pour les routes.
Convivialité à la fonderie
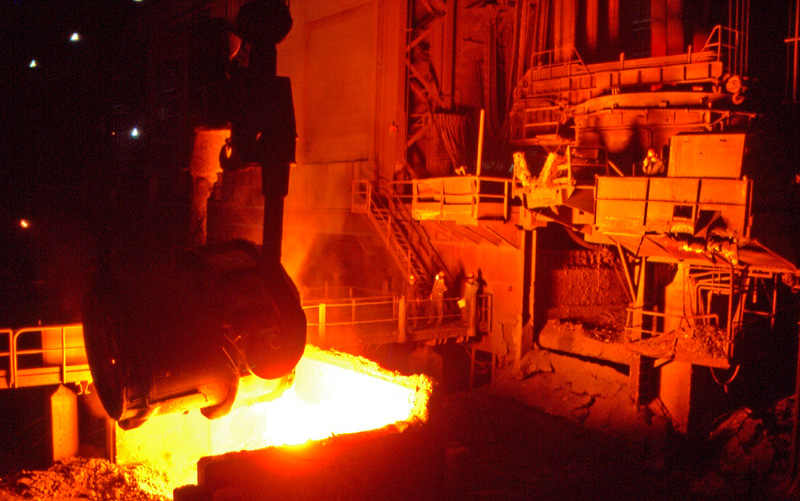
Les aciéries : de la fonte à l’acier
Bien que l’on puisse la produire en grandes quantités, la fonte a ses limites : elle est très lourde et très cassante, on cherche donc à la transformer en acier. En 1888, l’installation du premier four Martin dans la région permet la production de l’acier à Pompey.
- A la sortie du haut fourneau la fonte est placée dans une grande cuve dans laquelle on injecte de l’air froid sous pression. Cette cuve est appelée four ou convertisseur.
- L’oxygène diminue la teneur en carbone de la fonte et la transforme en acier. Il élimine également les impuretés comme le phosphore ou le silicium.
1895 : création d’une aciérie Thomas à Pompey qui permet l’utilisation du minerai phosphoreux appelé minette très présent en Lorraine. On ne pouvait l’utiliser auparavant car lors de la combustion, l’acide phosphorique dégagé par le minerai détruisait les fours. Cette installation signe l’abandon définitif du fer puddlé et augmente largement les capacités de production.
Les deux hauts fourneaux datant de 1872 et de 270m cubes ne suffisent plus à approvisionner le four Thomas. En 1900, deux hauts fourneaux de 500m cubes chacun sont alors construits.
Le four Thomas installé en 1895 est seulement remplacé en 1964 par une aciérie à oxygène (aciérie LD) beaucoup plus moderne. Depuis sa cabine, l’opérateur LD est en charge de l’élaboration de l’acier :
- En fonction du type d’acier que l’on veut obtenir, les quantités de matières utilisées diffèrent : on utilise la fonte, la ferraille, des alliages…
- Dans les années 70, l’usine de Pompey fabrique 250 nuances d’acier différentes.
On produit par exemple de l’acier à haute élasticité pour fabriquer des ressorts. A Pompey on pouvait fabriquer de minuscules ressorts pour les douilles des lampes ou les serrures de voitures, et d’immenses ressorts de deux mètres. En 1874, les aciéries de Pompey ont produit 29 000 tonnes d’acier pour ressorts.
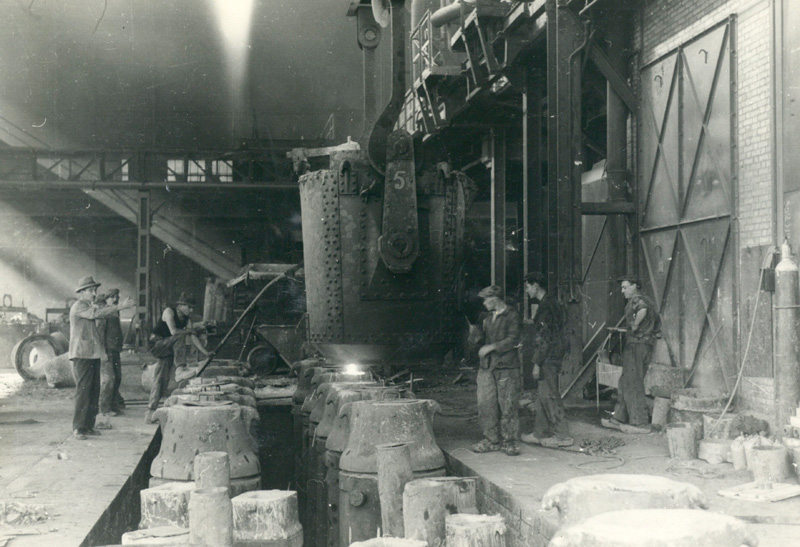